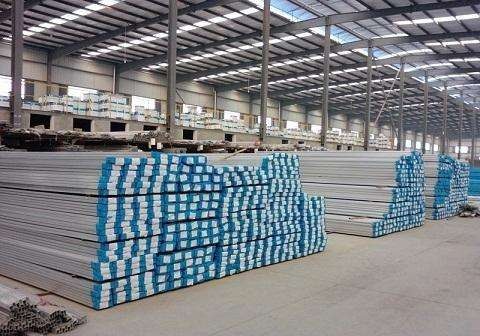
Aluminum extruding is one of the traditional metal work methods, but sometimes you can find that some extruders make their aluminum extrusions with low quality, they may tell you the items are not used for exacting jobs so that they are acceptable. However, you always need to take very care of your custom aluminum projects, here we list some features of poor quality aluminum extrusions below for your reference.
1. Too thin anodic oxidation coatings
The GB Standard requires the anodic oxidation coatings of structural aluminum extrusions can not be less than 10um (micros). The extrusions would be rusty and corruptible easily if the thickness of coating is not enough, but some aluminum extruders made their extrusions with the anodic oxidation coatings below 4um or without the coating while it is needed. It is estimated that the anodizing process would cost $25 USD per ton for increasing 1um anodized coating on the extrusions.
2. Unqualified chemical composition
It would save the material cost if the aluminum alloy is mixed with certain amount of aluminum scrap or impurity aluminum, but it will lead to unqualified chemical composition for the structural aluminum extrusions and seriously endanger the structural projects.
3. Reduce the wall thickness of aluminum extrusions
According to the GB standards the wall thickness of aluminum extrusions for 90 series sliding windows can not less than 1.4mm, but in fact some China aluminum extrusion used for these products are just between 0.6 to 0.7mm. Some of the 46 series door extrusions are with thickness of less than 1.2mm while the GB standards define they must be up to 1.62mm.
|